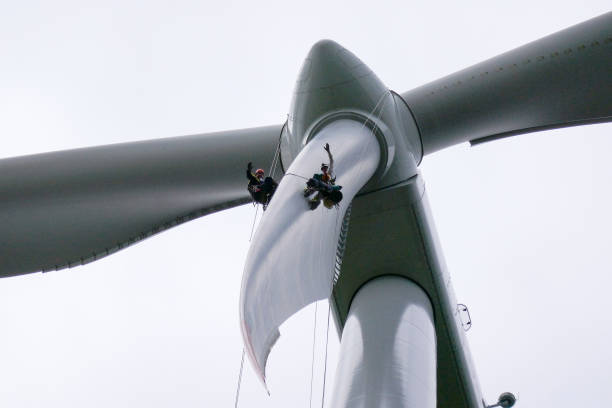
Wind turbines are some of the tallest and most complex structures architected by humankind. Whilst everyone is aware that their purpose is to harness wind energy, thereby providing clean electricity to numerous residential customers, the public knows very little when it comes to how these turbines are inspected and maintained.
The costs to bring a turbine down to the ground once it has become operational are rather high; therefore, since this technology came to life until today, companies have used the “tap test” to inspect the turbines and detect potential problems (Andreisek et al., 2016). The “tap test” is performed by wind turbine technicians, who get on top of the turbine, hang on ropes and tap along the helixes in order to detect any abnormalities. In case the “tap” inflicts a noise considered “abnormal” by the technician, the turbine is flagged for potential defects and brought down to the ground for further inspection (Andreisek et al., 2016).
Needless to say, this inspection method is not only outdated but it poses a life threat to the technician performing it. In addition, the method is an inadequate means of measuring the functionality of a turbine as issues are only detected in case the “tap” is different, thereby not allowing space for preventive measures.
To come to the aid of wind turbine operators, startups are racing to develop new technologies that can provide real-time data on the well-being of the turbines. One of the most original ideas, gathering considerable amounts of VC funding is that of turbine-crawling robots developed by BladeBUG (Hanley, 2021). BladeBUGs are set to replace wind turbine technicians as they will be placed in the blades to scan them through ultrasonic non-destructive testing, service mapping, localized mapping, and send the data to wind farm operators. This new method of testing will finally enable companies to harness the power of data and information systems to detect potential problems before they occur (Hanley, 2021).
Andreisek, G., Korthals, D., U. Grosse, C. and U. Seeber, B., 2016. The virtual tap test – a training system for wind turbine rotor blade inspectors. [online] 19th World Conference on Non-Destructive Testing 2016. Available at: <https://www.ndt.net/article/wcndt2016/papers/th4e3.pdf> [Accessed 27 September 2022].
Hanley, S., 2021. BladeBUG Inspects, Resurfaces, And Repairs Wind Turbine Blades Remotely. [online] CleanTechnica. Available at: <https://cleantechnica.com/2021/01/05/bladebug-inspects-resurfaces-and-repairs-wind-turbine-blades-remotely/> [Accessed 27 September 2022].
I had no idea wind turbine maintenance was so outdated. Out of curiosity, what is the cost to repair a wind turbine? Also, the car industry has had telemetric devices to inform the driver of when to go in for a service and if there is an issue the ‘check engine’ light turns on. So maybe automotive companies may have insights that are transferrable to BladeBUGs and the rest of the wind turbine industry.
Well, solely the maintenance of a turbine is estimated to be around $42,000-$48,000 per year, which is a number that could be substantially reduced if maintenance is fully (or even partially) automated. The cost for repairment on the other hand depends on the type of turbine (on/offshore) and where the issue has occurred; for instance, according to a research offshore wind turbines are likely to face 8.3 failures per turbine per year. That includes 6.2 minor repair (costs below 1000 EUR), 1.1 major repair (1000 +EUR), and 0.43 major replacement and 0.7 failures where no cost data can be categorized. Imagine these costs applied in a whole wind farm (i.e 100+ operational turbines).
Your recommendation is rather interesting! We should probably recommend the IS team to have a case study on digitizing outdated wind-turbine maintenance activities next year hahah